ShawX Manufacturing using Delhoist telescopic cylinders
05 December 2018
As a family-owned business, ShawX Manufacturing is the new force behind the specialist trailer manufacturer formerly known as Titan Manufacturing. Based in the Brisbane suburb of Cleveland, the change of ownership and establishment of a new management team is building the company by drawing on real-world working industry knowledge to design and construct equipment for the earthmoving and construction industry.
Since taking over Titan Manufacturing some two and a half years ago, ShawX manufacturing has forged a solid reputation for the quality design and manufacturing of earthmoving equipment attachments, including rippers, hitches, buckets, single, bogie and tri-axle tag float trailers, tipper bodies, and, its latest design innovation, the EjectX body truck.
Kenny Shaw, his wife Donna and their two sons, Brett and Jacob, make up the team and oversee approximately 20 employees.
Kenny and Brett are both qualified diesel fitters and boilermakers, and have worked extensively in the earthmoving industry all over Australia, giving them hands-on experience and the ability to identify shortcomings with equipment design to manufacturing components that work and last the distance. Not surprisingly, this experience enables them to use the phrase “From the industry “ For the industry”, to position their business in the minds of their customers.
PowerTorque spoke with Brett Shaw at the recent Diesel, Dirt and Turf Expo, held at the Penrith Panthers complex in Western Sydney.
“We have, over the years, seen all manner of equipment fail and wear out prematurely in our own earthmoving business, in which we still have a working interest. Experiencing these problems firsthand resulted in the need for us to either re-engineer or repair substandard equipment in order to get the job done. We find this puts us in a unique position to manufacture equipment that works, which is built to a robust standard and not down to a price. We manufacture equipment that we would want to use ourselves,” said Brett.
“We are passionate about the Australian manufacturing industry, we design and construct for quality and functionality, whilst utilising Australian-sourced materials and components wherever possible. BlueScope Steel products are used when applicable and we use Delta Hydraulics based in Devonport, Tasmania, for our hydraulic rams and associated equipment. Delta is a large, Australian-owned company employing over 100 staff, and provides us with a great service, plus they are very easy to deal with,” said Brett.
ShawX Manufacturing utilises a machine shop, C.N.C control systems, profile cutters and its own paint shop to manufacture its products. It also carries out repair and modification work to all manner of equipment and implements for the earthmoving and construction industry.
Trailer and tipper body manufacturing is also a key feature of the ShawX range of products. Tag plant trailers are built to customers’ needs with individual and unique designs that cater for single, bogie and tri-axle configurations. These feature a heavy-duty integrated beam chassis, ABS braking, electric or hydraulic ramps, welded cleats on ramps for added traction, and LED lighting. Options include oversize packs, hammer wells, hydraulic winches and sliding draw toolboxes.
ShawX tipper bodies feature all Bisalloy construction in standard or custom-made sizes, two-way tailgates, internal tie-downs, LED lighting, 2pac paint and internal steps.
A new innovation in bulk earthmoving and construction material transport and handling has been gaining traction for ShawX Manufacturing in the form of its EjectX body truck. When taking a quick glance, it looks very much a standard tipper truck, but, on closer inspection, there’s a huge difference “ this tipper doesn’t tip.
Brett explained: “With safety as a main driving force, we developed the EjectX to provide a viable transport option while improving safety. By negating the need to raise a body, and thus risk the chance of rollovers during the discharge process, we see this type of design creates a greater operating range with the ability to eject loads on adverse slopes, under power lines, bridges and low tree canopies, where conventional tippers cannot operate”.
“Our EjectX design utilises a horizontal plough blade running along internal guide rails controlled by a Delta Hydraulics double-acting ram along its length to eject the load from the rear of the body. The ten-wheeler models utilise a 40-tonne ram, with 25-tonne and 20-tonne rams for the eight and six-wheeler versions.
On show at the National Diesel, Dirt and Turf Expo was an EjectX body fitted to an Isuzu FX series ten-wheeler rigid truck with a cubic capacity of 18 cubic metres and a payload of 18.5 tonnes. Throughout the show, Kenny Shaw highlighted the efficiency of the design to completely empty the bin by throwing a handful of coins inside and successfully pushing them out with the plough blade. Only problem with that was, the inquisitive kids watching on were a little quicker than Kenny at retrieving the displaced coins.
“The plough has heavy-duty skirt rubbers fitted to its base and sides. We see these as having a service life of around four to six months, depending on the material being handled and the operating cycles. These skirt rubbers are easily operator-replaced when required. There is also a return rubber located on the rear of the plough, so that if any product has fallen behind the blade during the loading process it is dragged back and ejected out by way of the two floor openings at the front of the floor. The plough blade then returns to its resting position conveniently covering over the hydraulic tank hoses and valving in the process,” explained Brett.
Stiffening ribs are used to reinforce the side walls, and specially-designed combing rails made to a point are featured to prevent product holding or sticking to the top rail, removing the need to brush off loading spill from top rails before transit. Tarps by Retractable Tarps of Brisbane control air-borne dust, and recessed clearance lights feature a protection rail to prevent damage by falling debris.
The first EjectX truck was put into service 18 months ago by G&H Civil Contractors Demolition and Plant Hire of Brisbane, with strong success. So much so, that, after a few minor design changes along the way, G&H Plant Hire now has six of these units operating 24 hours a day, asphalting at night and on construction and demolition work during the day, with prime contractors requesting as many of the EjectX trucks as they can supply, as work dictates.
G&H Plant Hire has confirmed the specific benefits of using the EjectX trucks for asphalting work on the Jupiters Casino complex, which required asphalting to be done under the canopy of an awning, which ruled out conventional tipper trucks on the job.
The Toowoomba Second Range Crossing project, which has unfortunately seen numerous tip-overs during its construction, is also keeping the six G&H Plant Hire fleet of EjectX trucks extremely busy.
Brett Shaw explained the benefits further: “We believe that while there are other forms of design that can negate the need for raising a body to unload, such as walking-floor and conveyors, our design is extremely efficient with fewer moving, and, therefore, less wearing components. It features less cleaning than that of roller and slat designs and results in quicker turnaround and reduced downtime. Operator error and misjudgement of slopes during unloading are also removed, greatly increasing safety”.
“We believe that, sometime in the future, all tier-one jobs will contractually require the use of non-tipping trucks for safety and compliance,” added Brett.
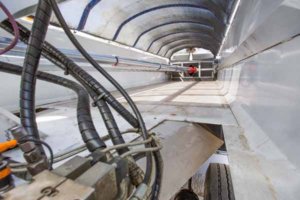
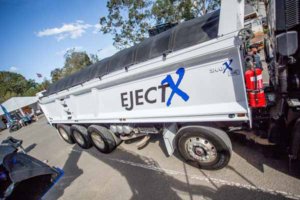
