Delta Hydraulics going the distance
01 September 2010
REGENCY PARK, SOUTH AUSTRALIA - Barry Stoodley Pty Ltd is currently enjoying its 30th year in the transport industry. Starting out in 1980, its aim was to provide the South Australian heavy transport industry with a professional alternative for the fitting out of prime movers and chassis modifications. As the company grew and developed into a manufacturer of specialised trailing equipment, the focus turned more towards the tipper market. With two branches in South Australia and a workshop in Brisbane, Barry Stoodley Pty Ltd is now one of Australia’s premier suppliers of transport equipment.
Part of the company’s success can be attributed to the selection of materials and components that can be depended on for reliability and durability.
Hydraulic cylinders by Delta Hydraulics are a product of choice for Barry Stoodley Pty Ltd and are used almost exclusively across the entire tipping trailer range.
“The Delta product is an excellent quality product and we specify Delta as standard equipment across our whole range of tippers,” says Norm Farnden of Barry Stoodley Pty Ltd. “The construction of the product and the use of micro finished hard chrome plating on each stage ensures a long service life. In addition to the hard chroming, the design of the seal allows the cylinder to continue working without any leaks. Once the cylinder is installed onto our tipping trailers, you can basically forget about them as they do not require any maintenance and are very long lasting.”
Delta Hydraulics designs and manufactures all of its hydraulic cylinders from its Devonport facility in Tasmania for use in various industries all over the world, with all cylinders manufactured to precise tolerances. It uses some of the most advanced manufacturing technology available, including state-of-the-art skiving-burnishing machines, CAD design, CNC lathes and CNC turning and machining centres. A computerised contract control and Quality Assurance system ensures that the relevant certification can be supplied with all components.
Amongst the products produced by the company are Delhoist Telescopic cylinders, Delhy Industrial cylinders, Delhy Mill and Semi Mill cylinders, hydraulic manifolds and integrated circuits. Delta Hydraulics can also manufacture hydraulic cylinders to suit customer drawings or requirements.
Delta’s Series 2000 Delhoist telescopic cylinder is the product used most widely by Barry Stoodley Pty Ltd and is the most popular product range manufactured by Delta. Available in TT (well mount) and BT (front of body) styles, the Series 2000 Delhoist telescopic cylinder has a maximum operating pressure of 3000 psi on 7 tonne through to 32 tonne rated cylinders; and 2500 psi on 45 tonne and 60 tonne rated cylinders. All stages are hard chromed for greater life and top sealing is finished with a technologically advanced twin lip seal. For added protection, the use of a ‘flapped’ wiper eliminates any moisture entry into the cylinder. A clip in base allows for easy assembly and servicing, and there is no need for the use of any gland nuts or a base plug. Other options available with this model include low profile foot mounts, a raised trunnion, hardened steel bushes, and bore sealed double acting on the last stage.
Barry Stoodley Pty Ltd operates a manufacturing and fitting workshop, and a hydraulics division in South Australia, both based in Regency Park. In addition to supplying the large number of cylinders required for the manufacturing facility, Norm and the staff at the hydraulics division carry an extensive range of Delta cylinders for retail sale and fitment to customer’s vehicles.
Norm comments, “The quality of the Delta product is great and our customers agree that Delta provides an excellent non leaking cylinder. As well as manufacturing a fantastic product, Delta also provides the service and back-up to match — providing technical assistance whenever it’s needed.”
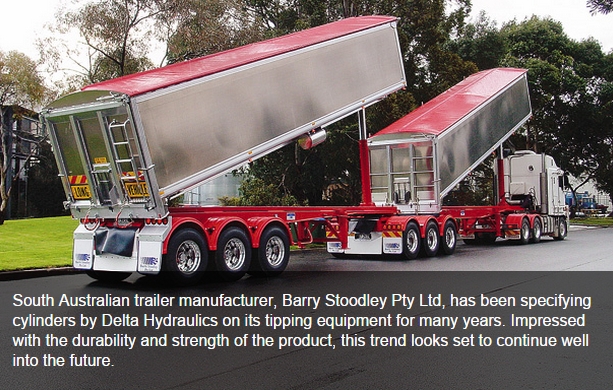
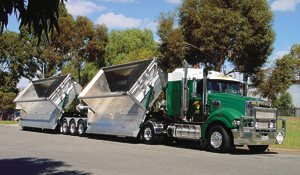
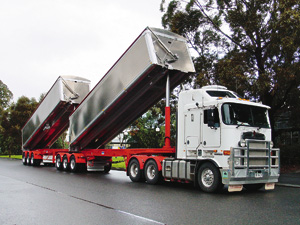